The operational dynamics of asphalt mixing plants can vary significantly based on their capacity. Understanding the differences in equipment failure rates and maintenance frequencies between high-capacity and low-capacity plants is essential for operators aiming to optimize performance and reduce costs. This article delves into these differences, providing insights for both large and small asphalt production facilities.
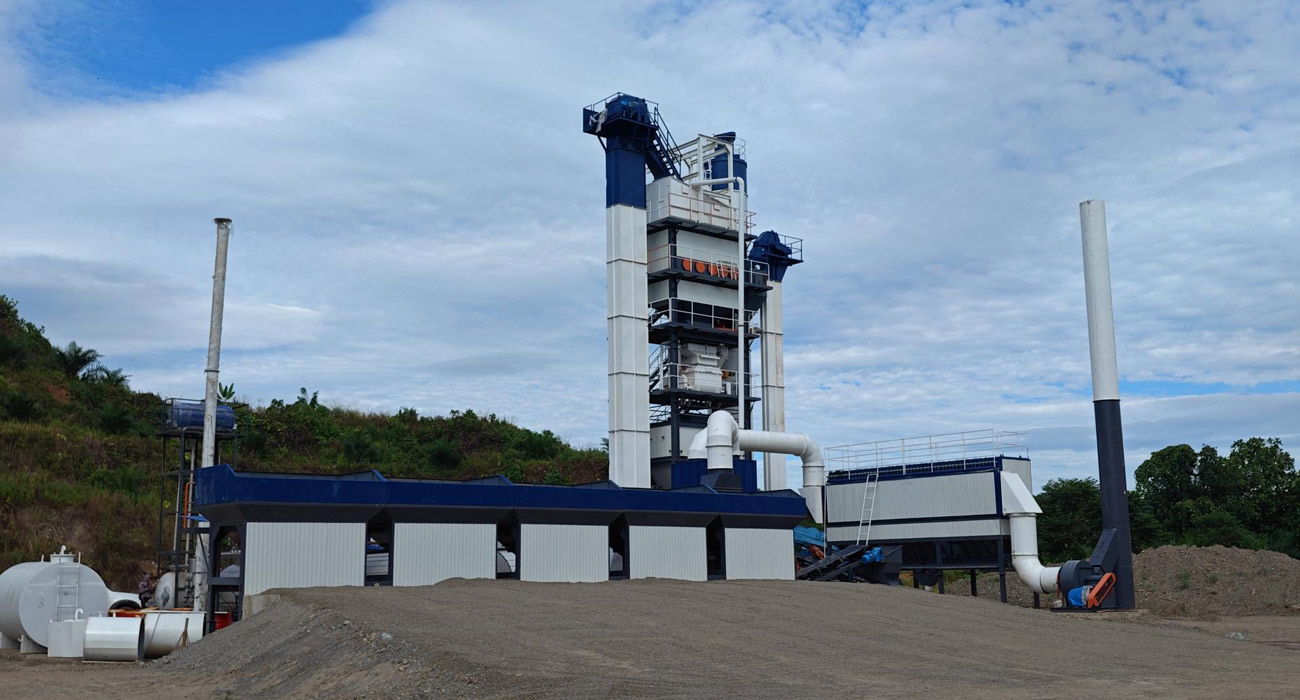
Equipment Failure Rates
High-capacity asphalt mixing plants, such as stationary asphalt plants, are designed for large-scale production. While they can handle significant output, the complexity of their systems often leads to higher equipment failure rates. These plants operate continuously under heavy loads, which can accelerate wear and tear on critical components. For example, the increased heat and stress on mixing blades and burners can result in more frequent breakdowns compared to low-capacity plants.
In contrast, low-capacity plants, including asphalt mixing plant portable, typically have simpler systems and operate at lower outputs. This reduced operational stress often translates to lower failure rates. However, it’s important to note that while these plants may experience fewer breakdowns, they can still face challenges in terms of equipment reliability, especially if not maintained properly.
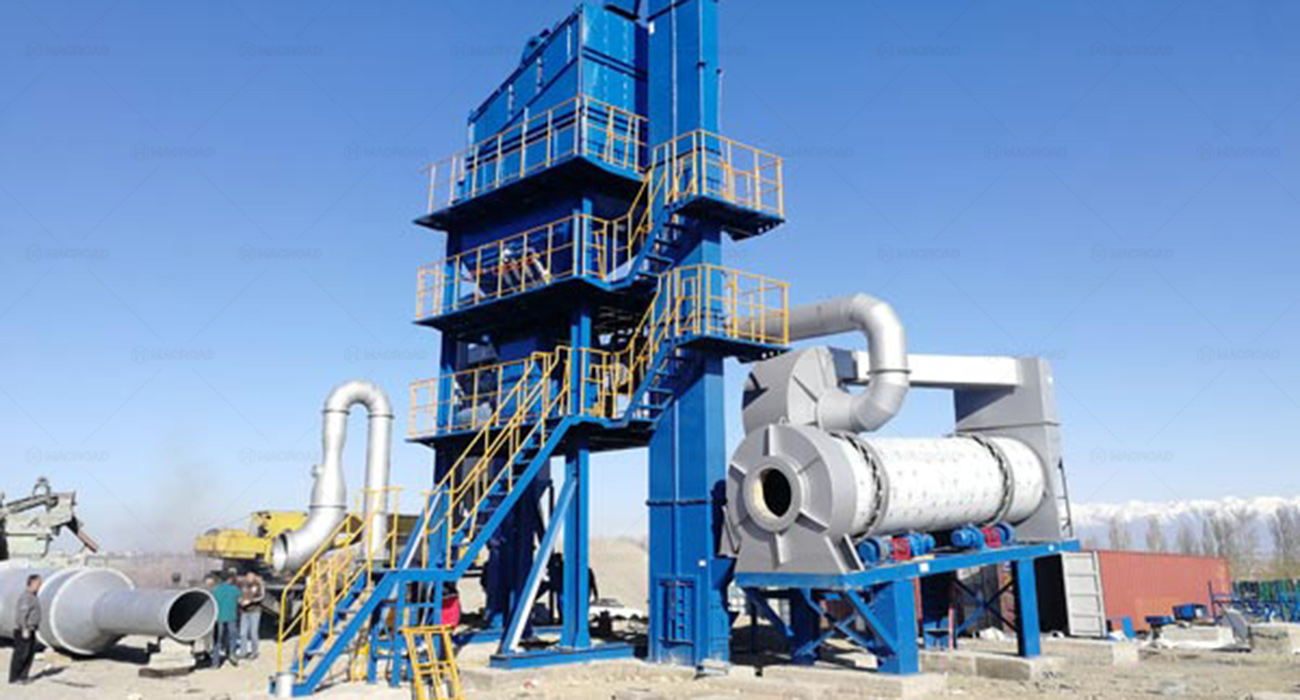
Maintenance Frequencies
The maintenance frequency of asphalt mixing plants is closely tied to their operational capacity and equipment complexity. High-capacity plants often require more rigorous and frequent maintenance schedules due to the high demand placed on their systems. Regular inspections, part replacements, and preventative maintenance are crucial to ensure that these plants continue to operate efficiently. For instance, drum mix asphalt plants may require more frequent checks on their heating systems and mixing components to prevent failures that could halt production.
On the other hand, low-capacity plants might have less demanding maintenance schedules. The simpler design of these plants allows for less frequent maintenance, but neglecting even minor issues can lead to significant downtime. For example, if a small portable asphalt plant has a clogged filter, it could affect production efficiency, leading to unexpected maintenance needs. Therefore, while maintenance may be less frequent, it remains critical for operational success.
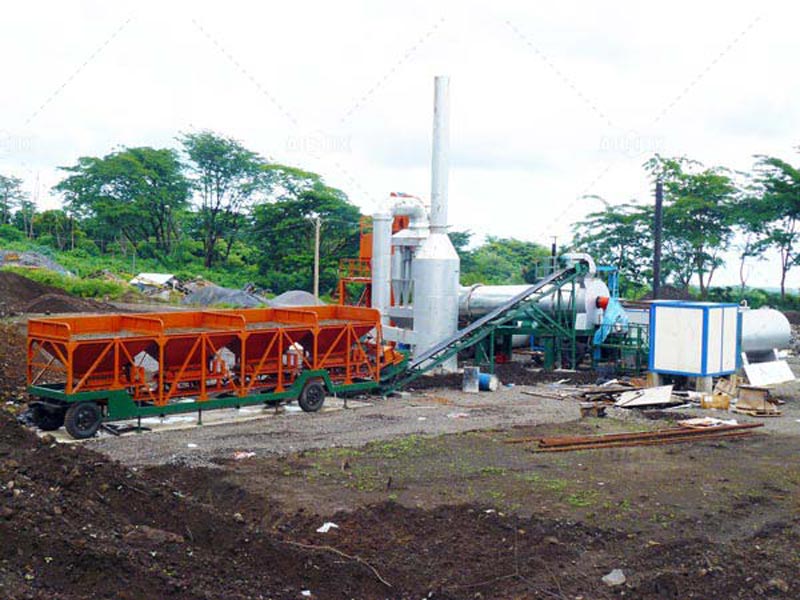
Implications for Operators
Understanding the differences in equipment failure rates and maintenance frequencies has significant implications for asphalt plant operators. High-capacity plant operators should invest in robust maintenance programs, ensuring they have the necessary resources for timely repairs and part replacements. This proactive approach can minimize downtime and enhance productivity, ultimately leading to better profit margins.
Conversely, operators of low-capacity plants should focus on routine inspections and preventative measures to ensure reliability. While their maintenance needs may be less frequent, remaining vigilant about equipment condition is essential to avoid costly failures.
In conclusion, both high-capacity and low-capacity asphalt mixing plants come with unique challenges regarding equipment failure rates and maintenance frequencies. By understanding these differences, operators can tailor their maintenance strategies to optimize performance, reduce costs, and ensure continuous asphalt production. As the industry evolves, staying informed about these operational dynamics will be crucial for long-term success.